Сотрудники из Университета штата Северная Каролина(США) опубликовали научный материал, в рамках которого описали простой и дешёвый способ изготовления кристаллов чипов. Подход значительно облегчает производство сложных нанометровых структур, что в теории позволит сделать выпуск микроэлектроники повсеместным и весьма недорогим явлением, что в корне отличается от текущей ситуации, где в руках всего пяти — семи компаний в мире собраны все возможности отрасли.
Итак, главное отличие нового метода от текущего, предполагающего выжигание структур лазерными сканерами — это заливка специальных форм уникальным металлическим сплавом(модифицированным вариантом металла Филдса — легкоплавким сплавом висмута, индия и олова), в момент затвердевания образующего необходимую конструкцию. Притом, обычные сплавы для реализации микроструктур полностью не подходят.
В момент изготовления чипа первоначально отлитой заготовке кристалла дают окислиться, после чего на неё наносят жидкость со специальными веществами, связывающими окислившиеся поверхности оксидами в единую крепкую пористую структуру. Далее полученную конструкцию заливают другой специальной жидкостью с растворённым металлом, который и заполняет пустоты в пористой структуре, а после испарения жидкости затвердевает и прокаливается при температуре 600 градусов по Цельсию. После проделанных операций, исследователи получили полностью работоспособную конструкцию способную к вычислениям на том же уровне, что и кристалл созданный на литографическом сканере, но в разы быстрее и дешевле.
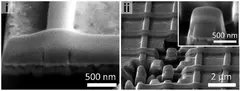
Минусы
Главным недостатком новой технологии является ограниченность исполнения в плане толщины нанометров. Учёным удалось исполнить эксперимент в диапазоне 44-1000Нм, что значительно более отсталые значения нежели применяемые для выпуска CPU/GPU теми же TSMC и Sansung 3-4Нм(чем меньше число тем совершеннее технология).
С другой стороны, абсолютное большинство бытовой техники использует техпроцессы в диапазоне 45-300нм, а значит новый метод способен снизить себестоимость очень многих вещей.
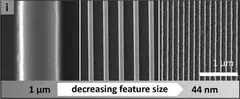
Источник новости: amd.news